Do Grinding Ball Sizes Determine Different Outcomes?
When it comes to choosing your custom ball mill for material processing, the size and type of grinding media you use play a crucial role in determining the efficiency, fineness, and quality of your end product.
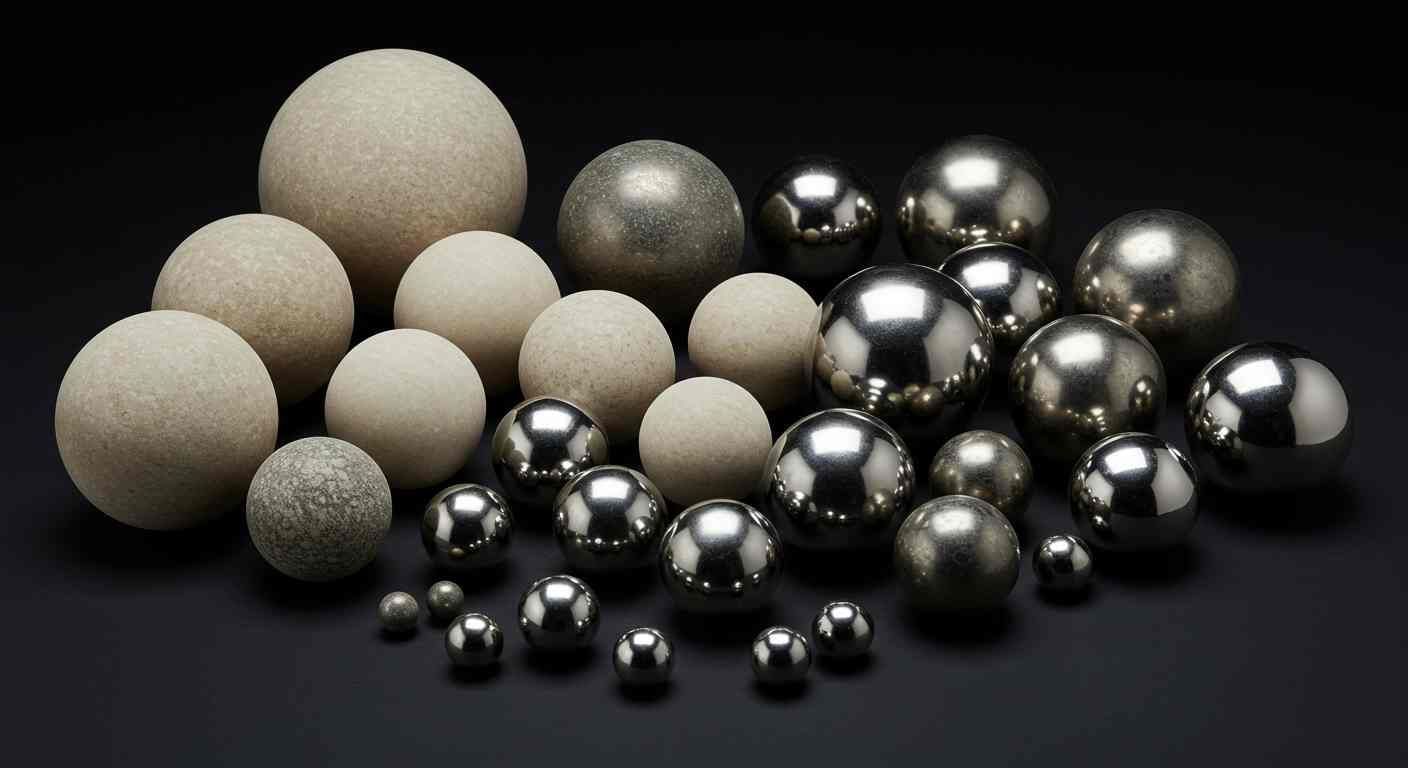
Whether you're processing limestone or other raw materials or processing fly ash, selecting the right grinding balls can make all the difference.
At Economy Ball Mill, we specialize in manufacturing custom ball mills for industries like construction, mining, and manufacturing across a wide scope of industires. One of the most common questions we receive is:
How Does Grinding Ball Size Impact Milling Efficiency?
The size of the grinding media directly influences several parts of the ball milling process:
- Particle size distribution
- Grinding efficiency
- Energy consumption
Let’s break down the key factors to consider when choosing grinding ball sizes for wet or dry ball milling.
What Is The Role of Large or Small Ball Grinding Media in Ball Mills?
Larger grinding balls best for coarse grinding and smaller balls are best for finer particle sizes.
Larger balls for ball mills have a heavier weight than smaller balls from the same media. This allows them to deliver a higher-impact force, which can break down larger particles more quickly. However, larger balls can also produce a wider particle size distribution if used alone—though they can be more efficient for hard materials.
Smaller grinding balls are best for fine grinding or milling into powder because the more balls in the mix, the greater the surface area contact. This is great for industries requiring a high level of fineness in their end result, like fly ash processing and cosmetics. However, working with smaller grinding media may require longer milling times—though they will yield a more consistent product.
Depending on your material, a mix of large and small grinding balls can balance the overall impact for a more uniform output
Does Media Size Change the Nature of Wet vs. Dry Ball Milling?
For wet ball milling, in many circumstances, smaller media often works and is more consistent because the liquid slurry helps reduce heat can prevent overgrinding by cushioning the impact of grinding.
Larger media may be more effective for breaking down dry materials—though the friction presents a higher risk of heat buildup, so media selection must balance the effects of friction, impact, and cooling.
Optimal Grinding Ball Size for Your Application
Material selection matters a lot when you’re considering the efficiency of your ball mill media. Harder materials need larger, denser grinding media, which is why stainless steel is a better choice than ceramics for products with a high hardness.
Steel or ceramic balls each have different wear rates and efficiencies to consider as well. Other factors like the desired fineness of the end product and the speed of the mill are also part of the final decision-making process.
Common Mistakes When Choosing Grinding Media
- Using Only One Ball Size – Keeping a mix of sizes on-hand and experimenting with different sizes and weights will help you choose the right option and improve your overall grinding efficiency.
- Ignoring Wear Rates – Monitor the wear rate of your ball mill lining and on your ball milling media. Taking the time and money for potential replacement may be a burden on your production timeline.
- Overloading the Mill – Too many balls or the wrong selection of ball milling size can reduce grinding efficiency.
Let Our Team Help You Find the Right Option for You
The right grinding media size is critical for achieving the desired particle size, minimizing energy consumption, and extending the life of your ball mill and liner. Whether you're processing limestone, fly ash, or manufacturing material for various industrial uses, our team at Economy Ball Mill can help you design a system tailored to your needs.
We serve clients from around the world at from our location in Tollesboro, Kentucky. Contact us online or give call us at (606) 798-5724 to receive expert advice on grinding media selection. A member of our team is standing by to discuss your ball milling requirements!