The Future of Cement Plant Equipment: Ball Mills for Grinding Cement
Ball mills are the essential to cement production, pulverizing clinker and additives into the fine powder essential for high-quality cement.
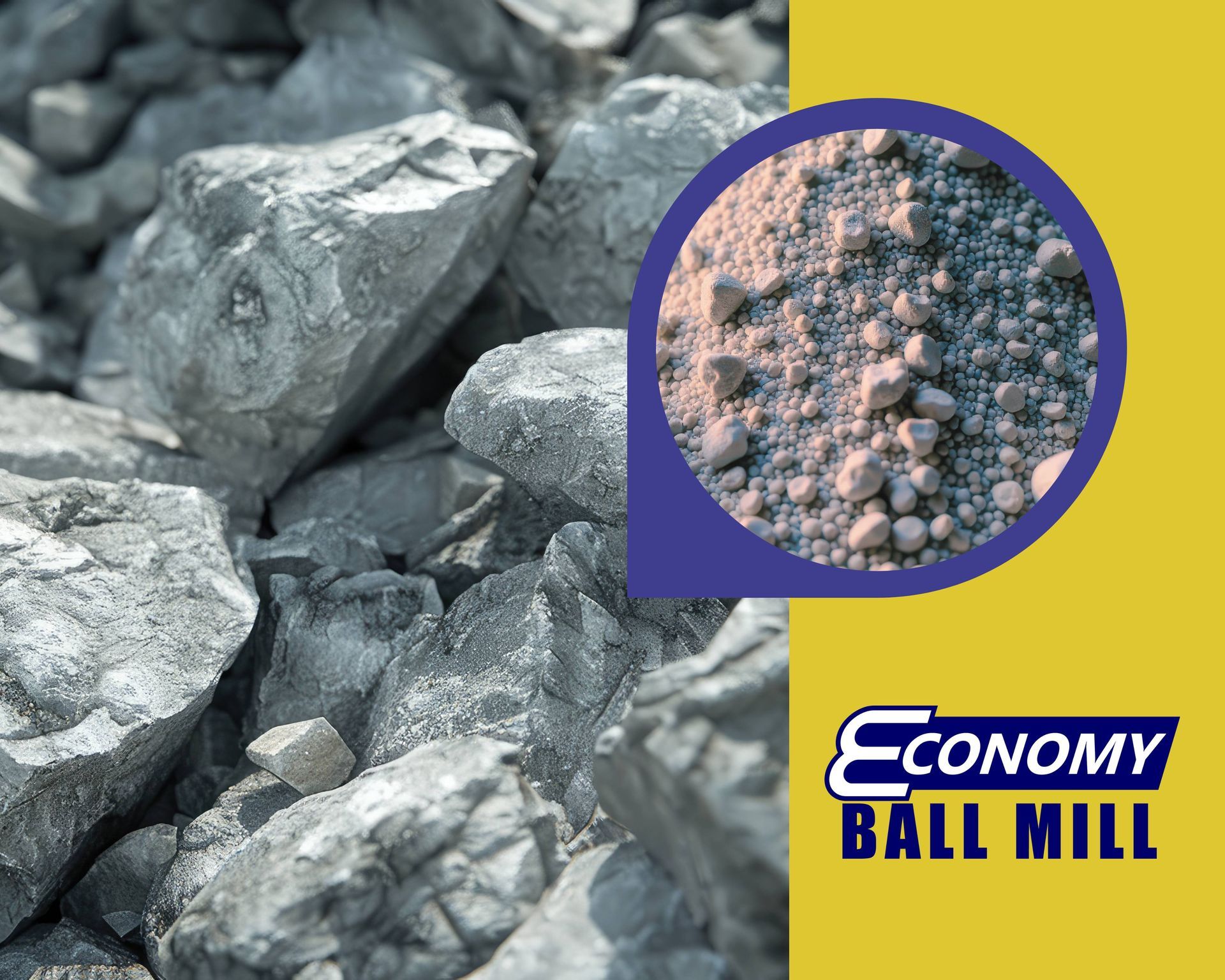
As part of your plant equipment, you may use vertical roller mills (VRMs) for raw material processing. Ball mills are the preferred addition for those who take on the process of grinding due to their unparalleled ability to deliver precise particle size distribution (PSD) critical for cement strength, setting time, and workability. In fact, cement grinding consumes up to one-third of a plant’s total electrical energy—highlighting why optimizing this process is paramount for profit and sustainability.
Unlike some alternatives, ball mills efficiently handle diverse feed materials—including clinker, gypsum, slag, pumice, and limestone—without compromising grindability or final product integrity. Their mechanical design ensures operational stability with lower maintenance complexity, particularly when processing abrasive clinker material.
Custom Ball Bills After Raw Milling
Combining ball mills with pre-crushers (e.g., roller presses) or high-pressure grinding rolls (HPGRs) boosts throughput from raw meal prep to cement grinding by 30–50% while lowering specific energy use. This approach leverages each technology’s strengths—HPGRs for coarse reduction and ball mills for precision finishing.
Why Economy Ball Mill Is Your Partner in Modernization
Economy Ball Mill delivers bespoke solutions tailored to your plant’s unique constraints:
- Custom-Engineered Mills: We design mills optimized for your clinker chemistry, target fineness, and throughput—whether for Portland, slag, or pozzolanic cements.
- Wet/Dry Process Expertise: Our mills handle both processes, with wet grinding ideal for limestone/slag (reducing dust) and dry systems minimizing post-grinding costs.
- Proven Testing Services: Test your materials first! Our onsite 20"x28" horizontal test mill (requiring just 10 gallons of material) replicates full-scale results for just $1–$2/lb. Scale up batches 6x larger for seamless process validation.
- Lifecycle Support: From corrosion-resistant liners to pinion gear overhauls and attritor mill barrel rebuilds, we maximize equipment longevity and minimize total cost of ownership.
- Flexible rentals: ($6,000/month) for immediate relief.
Your Strategic Imperative: Modernize or Fall Behind
Cement producers face mounting pressure to cut CO₂ emissions and energy costs while meeting rising demand. With fly ash supplies drying up as coal plants shutter, modern ball mills are still vital assets that deliver:
- Enhanced Flexibility to grind sustainable alternatives like pumice or slag without quality loss.
- Future-Proof Compliance with emissions regulations through efficient operation.
We don’t sell "standard" mills. Every Economy Ball Mill is custom built for your process:
- Material-Specific Design: for varying clinker hardness, target fineness, and additives to dictate your liner/media profile.
- Hybrid Circuit Ready: Integrations with roller presses or HPGRs for higher throughput.
- Lasting Support: Our Kentucky-based engineers provide lifecycle care—from installation to overhauls.
Ready to Transform Your Cement Grinding Process?
If your plant still struggles with high energy bills, inconsistent cement quality, or frequent mill downtime, the solution is clear. At Economy Ball Mill, our engineers build cutting-edge, custom ball mills to modernize your cement, clinker, or grinding operations from the ground up with rental ball mills and grinding process development and testing.
Contact us online or call (606) 798-5724 to learn more about your next custom ball mill solution from Economy Ball Mill!
We serve clients around the world from our site in Tollesboro, Kentucky and look forward to working with you.