Understanding the Parts of a Ball Mill
A custom ball mill is a complex machine meant for grinding or processing material for commercial or industrial uses. You might be interested in learning more about how a ball mill can benefit your business, or you could be a seasoned pro of the ball mill grinding process—but one common question we’re asked by many clients is for us to explain what a ball mill is like inside—describing its important parts and customizable options—so that you can learn more about what solution is best for your business.
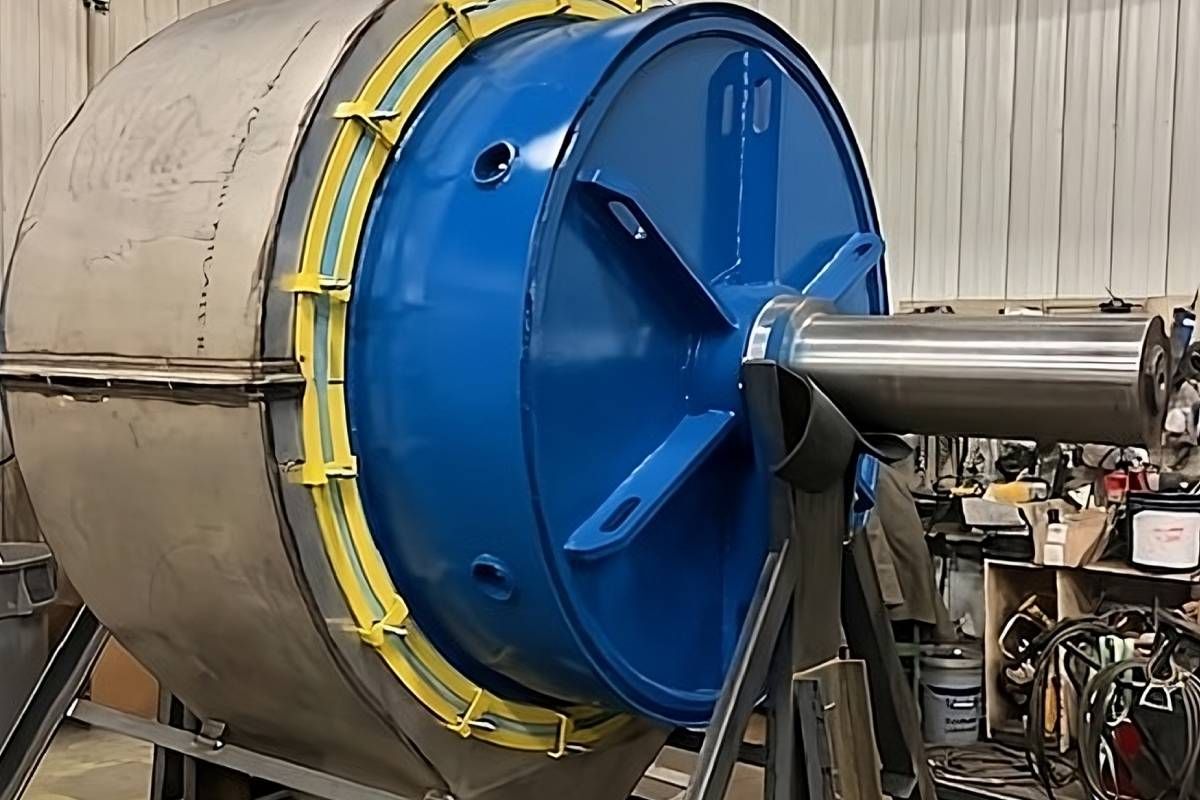
At Economy Ball Mill, our experienced team has over 50 years of experience in providing industrial solutions to business owners. Let us break down the parts of a custom ball mill and share some knowledge that may impact your next order.
The Parts of a Ball Mill
- The cylinder is the container that holds the ball mill grinding process together. We size cylinders by their total volume when empty. When selecting a cylinder, it’s important to pick a size that could potentially hold all of your grinding media, raw materials, and 25% of your total volume for processing space—what we consider the "working" area of the ball mill.
- Grinding media, also known as milling media, are the namesake balls of the ball mill. These grinding media are usually made from steel, glass, or ceramics, and you can choose a media material and ball diameter to customize how coarsely or fine you process your raw materials.
- Raw materials are what you charge into the ball mill to be processed. Raw minerals, metals, and plastics are some examples of the raw materials you can reduce to bring more of your manufacturing process in house.
- The motor and gearbox are part of the ball mill’s drive system. Depending on the size of your cylinder and the materials you are processing, you may need different types of motors and drive trains so that your ball mill is working its best. These may be belt driven, direct coupling, or ring and pinion driven.
- The discharge system is what removes the milled material from the machine. You can refine your discharge system to control the size of particles that the machine processes while retaining the grinding media for both wet and dry applications.
- The braking system positions and holds the ball mill so that it can be charged with raw materials or so that the processed materials can be discharged for further use.
What is a Pinion?
In the context of ball mills, a pinion is component of the drive system that runs in conjunction with the ring gear. It's typically connected to the gearbox and is responsible for transmitting rotational power to the mill. Proper design and maintenance of the pinion are essential for efficient mill operation and longevity of your ball milling equipment.
Types of Ball Mill Liners
Ball mill liners play a role in the grinding process and can shield the shell from wear and impact. Each type of liner has its advantages and is chosen based on factors such as the material being ground, desired fineness, style of grinding (wet vs dry), and other considerations. Some of the types of ball mill liners we provide are:
- Unlined Abrasion Resistant 400 (AR 400) Steel: The mill shell itself is constructed from AR 400 steel, eliminating the need for separate liners. This design may not be ideal for all types of grinding material or grinding conditions.
- Alumina Liners: Alumina are known for their wear resistance, though they can be more brittle than steel or rubber liners. They offer superior abrasion resistance and can significantly extend the time between liner replacements, reducing maintenance downtime.
- Rubber Mill Liners: Made from high-quality rubber compounds, they provide excellent noise reduction and are often lighter than steel or ceramic liners. They offer good impact resistance and can help protect the mill shell from damage.
Contact Us To Learn More About Your Next Ball Mill, Inside And Out
At Economy Ball Mill, we are your materials processing experts with the knowledge you’re looking for. We can help you create the perfect custom ball mill to your specifications or discuss how we can help you improve your materials processing with a new ball mill.
Contact us online or call (606) 798-5724 to learn more about our ball mills and how they work—both inside and out. We serve clients around the world from our site in Tollesboro, Kentucky and look forward to working with you.