Dry Ball Mill Grinding Vs. Wet Ball Mill Grinding
Dry grinding and wet grinding are two different methods of milling that have their own advantages and disadvantages. When you’re optimizing your grinding process for manufactory purposes, it’s vital to choose the right methods.
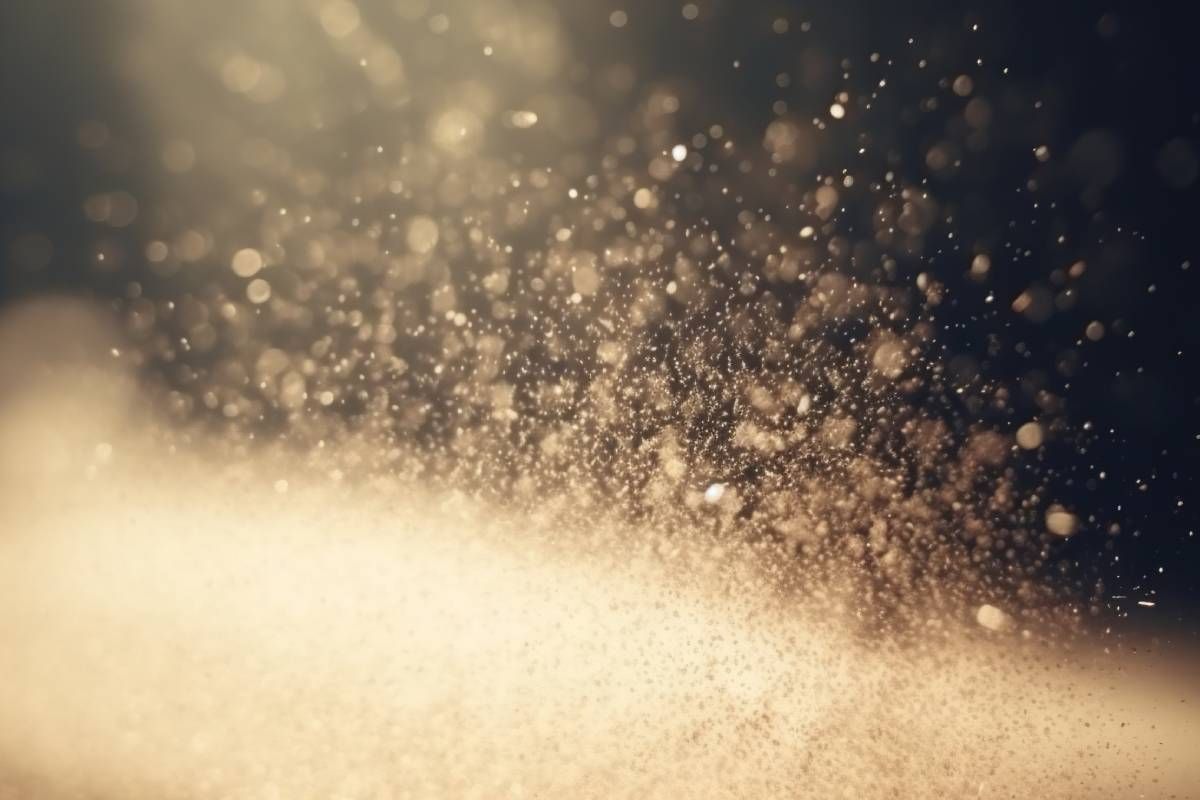
Let’s compare and contrast the two and look at how to choose the best one for your application.
Dry Grinding Machine vs. Wet Grinding Machine
To get a better idea of dry ball mill grinding and wet ball mill grinding, let’s first look at the differences between the two associated machines.
- Dry grinding machine: A dry grinding machine uses no liquid element and relies on particle-on-particle contact to reduce the size of the materials.
- Wet grinding machine: On the other hand, a wet grinding machine uses a liquid, such as water or solvent, as a lubricant and cooling agent to disperse the particles in a slurry.
The main difference between dry grinding and wet grinding is the effect of the liquid on the final product. Dry grinding produces a finer and more uniform particle size distribution, while wet grinding produces a coarser and more irregular particle size distribution.
- Dry grinding is more suitable for materials with low moisture content or are hard and abrasive.
- Wet grinding is more suitable for materials with high moisture content or soft and easy-to-break materials.
Dry Ball Milling vs. Wet Ball Milling
A ball milling machine is a device that uses balls, usually made of metal or ceramic, to grind the materials inside a rotating drum. The drum can be either horizontal or vertical, depending on the design of the machine.
The main difference between dry ball milling and wet ball milling is the energy consumption and the throughput.
- Dry ball milling requires less energy than wet ball milling but has a lower throughput.
- Wet ball milling requires more energy than dry ball milling but also has higher throughput.
Dry ball milling is more efficient for materials that don’t require very fine particles or have a low tendency to group together. Wet ball milling is more efficient for materials that require very fine particles or have a high tendency to collect.
How To Choose the Best Method For Your Application
There’s no definitive answer to which method is better for your application, as it depends on several factors, such as:
- The properties of the materials, such as moisture content, hardness, abrasiveness, etc.
- Desired particle size distribution and quality of the final product
- The availability and cost of the liquid element
- The environmental impact and safety of the process
You should consider all these factors before deciding on the best method for your application. That’s why you we offer consultations with our ball mill experts at Economy Ball Mill, who can help you find the best solution for your manufacturing needs.
Get Started with Economy Ball Mill Today
At Economy Ball Mill, we’re a leading manufacturer of custom-made ball mills for various industries. We have many years of experience in designing and producing high-quality ball mills that can meet your specific requirements. We can provide both dry ball mills and wet ball mills, and can complete attritor mill barrel rebuilds.
We’re based in Tollesboro, Kentucky, but we serve customers worldwide. We do not offer on-site installation or transport of our products, but we can ship them anywhere you need them.
If you are interested in our products or services, please contact us online or call us at (606) 798-5724. Our team is standing by to take your business to its next level with mall bills from Economy Ball Mill.